Unlock the world of shot peening with this complete guide. Learn about shot peening machines, their function, benefits, and how shot blasters contribute to industries worldwide.
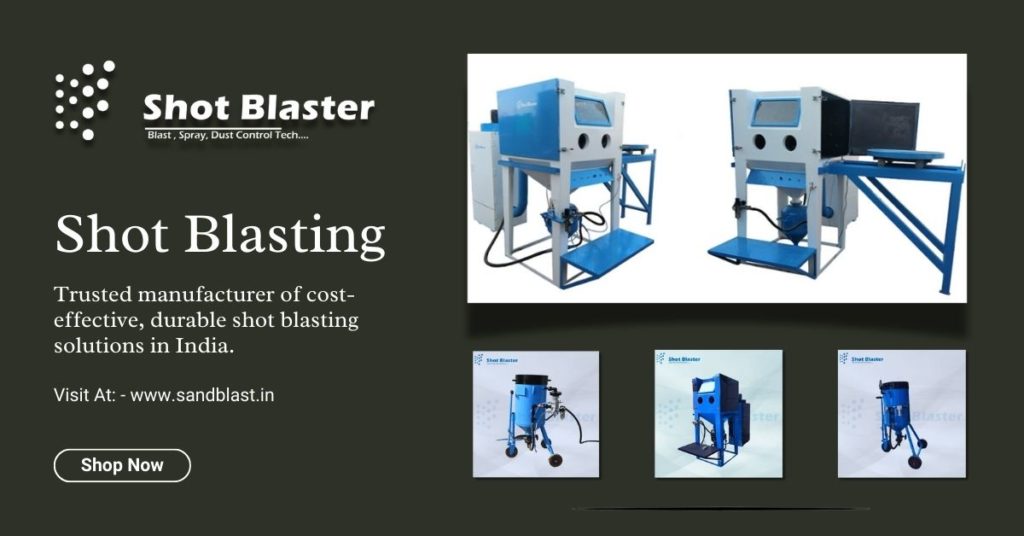
Introduction
If you’ve ever wondered how metal parts, aircraft components, or even tools gain their durability and resistance to wear and tear, shot peening might just be the answer. In simple terms, shot peening is a mechanical process that involves bombarding a surface with small metallic particles—shots—to enhance its strength and longevity. It’s a critical process used in many industries, from aerospace to automotive manufacturing. The machines that perform this task are called “shot peening machines or shot blasters,” and in this guide, we’re going to dive deep into understanding them.
From the basic mechanics to advanced applications, this comprehensive guide will give you all the info you need to understand the fascinating world of shot peening machines and shot blasters. Ready to explore? Let’s get started!
Also Check – Shot Blasting Machine | Shot Blasting Machine Manufacturer | Buy Shot Blasting Machine
What is Shot Peening?
Shot Peening Basics
At its core, shot peening is a process that improves the mechanical properties of materials by inducing compressive stress. But, what does that mean? Well, when a part is exposed to repeated stress or load, it can form tiny cracks and become more prone to failure. Shot peening helps prevent these issues by introducing compressive forces on the surface of the material, making it more resistant to fatigue and stress corrosion.
The process involves spraying thousands (or sometimes millions) of small metallic particles—called shots—onto a surface. These shots can be made of various materials, including steel, glass beads, or ceramic. When they strike the surface, they create small indentations that produce a layer of compressive stress. This layer significantly improves the part’s durability and resistance to cracks, pitting, and other forms of wear.
Why Shot Peening is Important
Shot peening plays a crucial role in improving the lifespan and performance of products used in harsh conditions, such as:
- Aircraft components
- Automotive parts (suspension springs, gears, etc.)
- Medical devices
- Industrial machinery components
- Oil and gas drilling tools
By enhancing fatigue resistance, shot peening is a game-changer for industries where precision, durability, and performance are non-negotiable.
Gain expert insights – https://riyasingh258.blogaaja.fi/the-future-of-surface-finishing-with-airless-shot-blasting-solutions/
How Shot Peening Machines Work
Key Components of Shot Peening Machines
Shot peening machines, also known as shot blasters, come in various types and sizes depending on the complexity of the application and the parts to be treated. But no matter the type, all shot peening machines share some key components. Here’s a breakdown:
- Hopper
This is where the shot material (metallic or ceramic beads) is stored before being blasted onto the part. The hopper often includes a mechanism to feed the shots at a controlled rate.
- Wheel or Nozzle
The heart of the machine, this is the part responsible for propelling the shots toward the workpiece. It uses high-speed rotation or compressed air to shoot the material with great force.
- Workpiece Holder or Conveyor
This is where the part being treated is placed. In larger systems, the part might be automatically moved along a conveyor belt, while smaller systems may require manual placement.
- Air or Mechanical Control System
This system regulates the speed and volume of the shots, ensuring consistency and efficiency during the peening process.
- Dust and Debris Collection
Shot peening generates a lot of dust and debris, so a high-efficiency collection system is vital for maintaining a clean workspace and ensuring safety.
Types of Shot Peening Machines
There are several types of shot peening machines, each suited for different needs. Here are the most common types:
- Airblast Shot Peening Machines: These use compressed air to accelerate shots toward the workpiece, making them perfect for small parts or delicate applications.
- Rotary Barrel Shot Peening Machines: Ideal for smaller parts that require thorough coverage, this type uses a rotating drum to expose the parts to the shots.
- Spinner-Hanger Shot Peening Machines: Typically used for larger, more complex parts, this machine uses a rotating hook to hold the workpiece while shots are blasted at it.
- Centrifugal Shot Peening Machines: These machines use a high-speed rotating wheel to throw the shots at the part, making them ideal for higher production rates.
Also Check – Shot Blasting Machine Manufacturers in India | Shot Blasting Machine for Sale
Benefits of Shot Peening
Shot peening isn’t just about strengthening metal parts—it offers a host of other benefits that contribute to the overall performance and cost-efficiency of manufacturing processes. Here’s why it’s so important:
- Increased Fatigue Resistance: The primary benefit of shot peening is the improvement of fatigue resistance. Parts that undergo shot peening are less likely to fail under stress and can last significantly longer.
- Reduced Stress Corrosion Cracking: By creating a compressive layer, shot peening minimizes the risk of stress corrosion cracking, particularly in materials like stainless steel.
- Improved Surface Finish: Shot peening can result in a smoother surface finish that reduces friction, wear, and tear during use.
- Enhanced Durability: Parts treated with shot peening are generally more resistant to fatigue, cracks, and other forms of failure, which is vital for critical applications in aerospace and automotive industries.
- Cost Efficiency: While the initial setup of a shot peening machine might seem like an investment, the long-term benefits—including longer-lasting parts, fewer failures, and less downtime—make it a cost-effective solution.
Learn from the best – https://riyasingh258.blogaaja.fi/how-to-choose-the-right-shot-blasting-machine-for-your-needs/
Applications of Shot Peening Machines
Shot peening machines are widely used across various industries. Their applications are diverse, making them essential in manufacturing processes where strength and durability are paramount. Here are some of the top industries that benefit from shot peening:
Aerospace Industry
In the aerospace sector, the performance of parts like turbine blades, gears, and landing gear components is critical. Shot peening is used to enhance their resistance to fatigue and stress corrosion, ensuring they perform reliably in the harsh environments of flight.
Automotive Industry
For automotive parts, shot peening improves the durability of components like suspension springs, crankshafts, and gears. It reduces the risk of component failure, which can be disastrous for vehicle performance and safety.
Oil and Gas Industry
In the oil and gas industry, shot peening is used to treat drill pipes, pressure vessels, and other critical equipment. These parts need to withstand extreme pressure and environmental conditions, making shot peening a valuable process.
Medical Device Manufacturing
Medical devices, such as implants and surgical tools, require exceptional strength and reliability. Shot peening ensures that these parts can endure stress over long periods without failure.
Also Check – https://rb.gy/ii4tpg | https://rebrand.ly/SB5asln | https://rebrand.ly/SB49Ind | https://cutt.ly/Ge9OZ25U
Frequently Asked Questions (FAQs)
What’s the Difference Between Shot Blasting and Shot Peening?
While the terms are sometimes used interchangeably, there’s a key difference: shot blasting is primarily used for cleaning or surface preparation, whereas shot peening is designed to induce compressive stress to improve the material’s strength and resistance to fatigue.
How Is Shot Peening Measured?
Shot peening is typically measured using intensity levels that quantify the size and number of shots impacting the surface. One standard measurement method is the Almen Strip Test, which evaluates the depth of the indentations created by the shots.
Is Shot Peening Only for Metal Parts?
No, shot peening can be used on a variety of materials, but it is most commonly applied to metals. Some ceramics and polymers can also undergo shot peening, though the process may require modifications.
Can Shot Peening be Automated?
Yes! Many modern shot peening machines are fully automated, offering higher production rates and consistent results. Automation can also reduce labor costs and improve overall process efficiency.
Also Check – Shot Blasting Machine Price | Best Shot Blasting Machine
Conclusion
In conclusion, shot peening is an indispensable process for improving the strength, longevity, and reliability of parts across various industries. Understanding the role of shot peening machines, or shot blasters, is crucial for anyone involved in manufacturing, as these machines are pivotal in creating products that can withstand the toughest conditions. Whether you’re in the aerospace, automotive, or medical industry, the value of shot peening cannot be overstated.
By following this comprehensive guide, you now have a solid understanding of what shot peening is, how it works, and why it’s so crucial in modern manufacturing. If you’re in the market for shot peening solutions, understanding these machines and their functions will certainly help you make an informed decision.