Shot blasting is a significant process applied across numerous industries for cleaning and preparing surfaces. In India, Shot Blaster provides top-notch shot blasting equipment solutions. This article examines their product range and clarifies how these tools enhance efficiency and quality across various applications. Whether involved in construction, manufacturing, or automotive, gaining insight into these solutions can guide you in selecting the appropriate tools for your requirements.
Let’s explore what Shot Blaster has available.
Understanding Shot Blasting Equipment Solutions in India
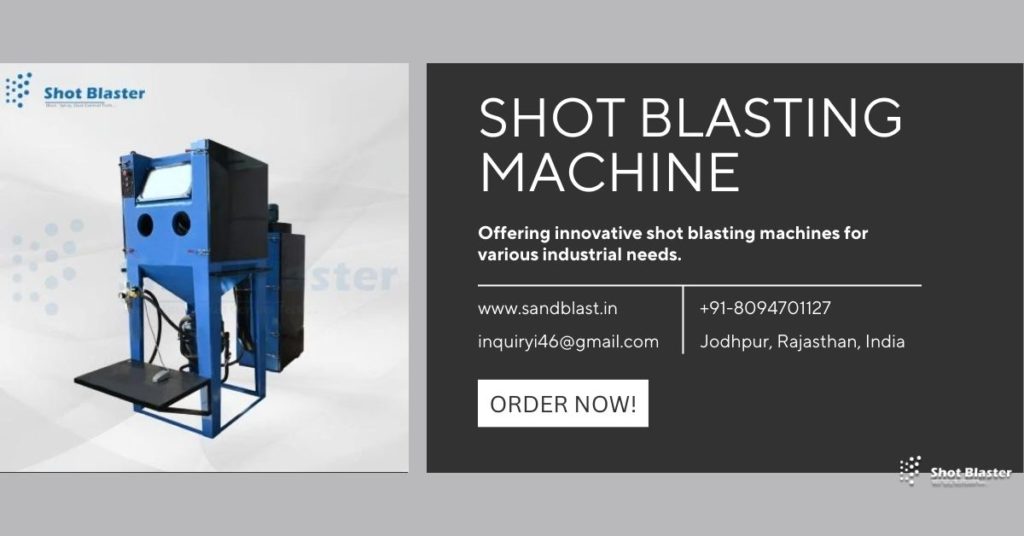
When selecting shotblasting equipment solutions in India, efficiency and maintenance factor into important choices. Durability and advanced technology are significant, as machines like shot blasting machines and sand blasting machines need to remove impurities effectively. Various types of machines, such as grit blasting and air blasting, serve different applications.
For instance, wheel blasting machines use centrifugal force to enhance surface preparation, while blast cabinets allow for precise polishing of metal. Trusted manufacturers create customized solutions that meet industrial needs and ensure customer satisfaction through quality control. They foster innovation, producing efficient equipment like manual shot blasting and shot peening equipment. The commitment to quality ensures these machines contribute to sustainability by improving operational effectiveness and extending metal strength while reducing metal fatigue during the blasting process.
Additionally, affordability influences choice, with many seeking preferred suppliers who offer a wide range of options, including steel shots and abrasives. The inclusion of compressors and bucket elevators enhances operational effectiveness, making these solutions important across every industry.
Also Check – Shot Blasting Machine | Shot Blasting Machine Manufacturer | Buy Shot Blasting Machine
Types of Shot Blasting Machines Available
Shot Blasting Machine
Selecting a quality shot blasting machine requires considering factors such as operational efficiency, customization options, and the type of abrasive media like steel shots or air blasting. Shot blasting has advantages over other methods like sand blasting by effectively removing impurities and enhancing metal strength. The blasting process provides superior surface finishing, which prepares metal components for further use, improves durability, and reduces metal fatigue.
For optimal performance, regular cleaning of the separator, inspecting the blast wheel for wear, and ensuring effective quality control practices are important. Manufacturers emphasize innovation and advanced technology that boost the machine’s efficiency and longevity. A commitment to quality in constructing shot peening equipment indicates that a reliable partner will help align machine costs with affordable prices while delivering customized solutions.
The incorporation of compressors and bucket elevators increases operational capacity while meeting every industry’s needs for surface preparation solutions. Manual shot blasting and blast cabinets cater to unique requirements, ensuring customer satisfaction with a variety of options tailored to specific applications.
Grit Blasting Machine
A grit blasting machine is widely used in industries for surface preparation, helping to remove impurities and improve metal strength. The blasting process can include various methods like shot blasting, sand blasting, and air blasting, each using different abrasive media. Compared to other machines, such as sand blasting machines, grit blasting machines often provide higher operational efficiency due to their innovative designs, including centrifugal force from blast wheels.
This advanced technology allows for better surface finishing and can enhance durability of metal components while preventing issues like metal fatigue. Regular maintenance practices, including quality control checks on components like separators and compressors, are important for longevity. Manufacturers enhance customer satisfaction through customized solutions, ensuring machines perform optimally over time.
Affordable prices paired with a commitment to quality make these machines a preferred supplier option for businesses across various sectors. The use of a bucket elevator in some models improves the handling of materials, showcasing a blend of functionality and sustainability in surface preparation solutions.
Also Check – Shot Blasting Machine Price | Best Shot Blasting Machine
Sand Blasting Machine
A sand blasting machine offers many advantages for preparing and finishing surfaces, such as removing impurities and enhancing metal strength. It is often used with steel shots and other abrasive materials in industrial settings to polish metal components and ensure quality control. When compared to other blasting methods, like air blasting or wheel blasting, a sand blasting machine frequently delivers a more efficient process and increased durability due to advanced technology.
Operators should prioritize safety by wearing suitable protective gear and ensuring proper ventilation to reduce dust exposure. Manufacturers focus on quality and sustainability by creating customized solutions to boost operational efficiency, using compressors and separators for effective abrasive recycling.
Various shot blasting machines, including manual shot blasting and shot peening equipment, are available at reasonable prices, making them reliable options for businesses across industries.
The blast wheel’s centrifugal force provides consistent results while prolonging the lifespan of machinery such as bucket elevators, important for maintaining productivity.
Related Article – https://riyasingh258.blogaaja.fi/reliable-shot-blasting-machine-provider-company-in-india/
Key Features of Shot Blasting Machines
Efficiency and Speed
The efficiency of shot blasting machines greatly enhances overall productivity in various applications such as surface preparation, metal finishing, and removing impurities from metal components. Factors like the power of the blast wheel, the type of abrasive media, and the design of the separator can influence the speed of the blasting process. By adopting advanced technology, like compressors and centrifugal force systems, manufacturers can optimize these factors for improved performance.
Innovations in shot blasting, including the use of steel shots and manual shot blasting techniques, also contribute to operational effectiveness and quicker results. This commitment to quality and speed leads to increased customer satisfaction and cost savings. Advanced shot peening equipment and blast cabinets ensure a high level of quality assurance, making them reliable partners in every industry.
The ability to customize solutions further enhances the blasting process, addressing specific needs such as surface hardening and polishing metal. Thus, advancements in technology and design directly enhance both the efficiency and speed of shot blasting equipment across industrial applications.
Dust Collection Systems
An effective dust collection system in shot blasting operations includes components such as separators, bucket elevators, compressors, and blast cabinets. These parts work together to remove impurities during the blasting process, whether using a shot blasting machine or a sand blasting machine.
The efficiency of these systems directly impacts the performance of shot blasting machines by ensuring that abrasive media like steel shots are delivered cleanly, which enhances surface preparation and polishing of metal components. Proper air blasting reduces metal fatigue and boosts metal strength while promoting safety.
Regular maintenance practices, such as inspecting the blast wheel and cleaning filters, are important for longevity and for ensuring that equipment operates at peak performance. Manufacturers who emphasize quality control and innovative solutions can offer customized options that meet the specific needs of various industries.
By integrating advanced technology and a commitment to quality, businesses can achieve operational efficiency and customer satisfaction while maintaining affordability and sustainability in their shot blasting endeavors.
Also Check – Shot Blasting Machine Manufacturers in India | Shot Blasting Machine for Sale
Durability and Maintenance
Shot blasting machines are built with durable materials and advanced construction techniques, incorporating high-grade steel and innovative coatings to ensure they last during operation. These machines withstand wear while preparing surfaces for various industrial tasks. Regular maintenance, ideally every few months, is needed for optimal performance and to avoid metal fatigue or failures.
Operators must be vigilant about issues like abrasive contamination or wear to the blast wheel, as these can hinder the blasting process and lower efficiency. Early detection of wear, including metal components losing strength or inconsistent polishing results, can help maintain performance. Commitment to quality and sustainability is important, and with proper care, these machines can deliver reliable surface finishing options. Manufacturers suggest that selecting the right abrasive media and thoroughly inspecting parts like the separator and bucket elevator can further avoid costly repairs.
Collaborating with a trusted partner enables companies to create tailored solutions that fulfill their requirements while ensuring the durability and performance of their shot blasting machinery at reasonable costs.
Popular Manufacturers of Shot Blasting Equipment in India
No.1 Manufacturer: Shot Blaster – Jodhpur, Rajasthan, India
This manufacturer combines advanced technology and innovation in their shot blasting machines, enhancing performance and efficiency. Shot Blaster use high-quality blast wheels and centrifugal force to optimize the blasting process, ensuring metal components achieve superior surface preparation. The durability and reliability of their machines stand out in various industrial applications, as they are designed to withstand heavy use and reduce metal fatigue.
Their commitment to quality is evident through rigorous quality control processes and the use of robust materials. Shot Blaster also offer a wide range of customized solutions, including sand blasting machines and shot peening equipment tailored to specific needs. Moreover, this manufacturer is a trusted partner to their customers, providing support and maintenance services to ensure optimal operation.
Shot Blaster prioritize customer satisfaction by delivering affordable prices and ensuring their products, like bucket elevators and compressors, perform efficiently for years. Their focus on sustainability and operational efficiency positions them as a preferred supplier in the market, addressing every industry’s abrasive blasting needs while maintaining metal strength and effectively polishing metal surfaces.
Also Check – https://rb.gy/ii4tpg | https://rebrand.ly/SB5asln | https://rebrand.ly/SB49Ind | https://cutt.ly/Ge9OZ25U
The Shot Blasting Process Explained
The shot blasting process involves several stages that enhance surface preparation efficiency.
First, metal components are placed inside a shot blasting machine where abrasive media, often steel shots, are propelled using a blast wheel or compressed air. This method effectively removes impurities and prepares surfaces for finishing. Shot blasting is often preferred over sand blasting due to its cost-effectiveness and better results in treating surfaces, such as polishing metal and improving metal strength through surface hardening.
In terms of equipment, manufacturers offer a wide range of customized solutions, including manual shot blasting and air blasting setups, ensuring that every industry can find suitable options that align with operational efficiency goals. Safety measures are important; operators must wear protective gear and follow guidelines to prevent risks associated with flying debris and noise.
Regular quality control checks on shot blasting machines and components help maintain durability and ideal performance. With a commitment to quality and sustainability, trusted partners in India provide innovative surface preparation solutions at affordable prices, fostering customer satisfaction.
Check out more – https://riyasingh258.blogaaja.fi/top-shot-blasting-machine-manufacturers-offering-affordable-solutions/
Benefits of Using Shot Blasting Equipment
Shot blasting equipment significantly improves surface preparation and cleaning processes by boosting efficiency and productivity. With various machines like shot blasting and sand blasting, manufacturers can select tailored solutions to meet their specific needs. This innovation facilitates quicker removal of impurities from metal components, enhancing the blasting process.
Advanced technology, such as centrifugal force in wheel blasting and air blasting, guarantees effective surface finishing, yielding higher quality and durability of products.
Additionally, employing steel shots and abrasive media allows the machines to harden surfaces, decrease metal fatigue, and polish metal components to a smooth finish. The commitment to quality in producing shot peening equipment also prioritizes safety. Equipment is crafted to operate securely with features that reduce hazards and encourage sustainability, such as efficient compressor and compressed air use.
This not only improves operational efficiency but also aligns with environmental practices, making shot blasting a reliable partner across industries for affordable prices and quality control.
Applications of Shot Blasting Equipment Solutions in India
Many sectors in India, such as automotive, manufacturing, and construction, are adopting shot blasting equipment to improve their operations. These applications aid in the maintenance and preparation of metal components, enhancing durability and strength. With advanced technology like shot blasting machines, manufacturers can achieve improved surface finishing and metal polishing while effectively eliminating impurities through the blasting process.
The integration of sand blasting and air blasting techniques enhances operational efficiency, leading to quicker cycle times and increased productivity. Indian manufacturers have reported notable advantages, including higher customer satisfaction and decreased metal fatigue, through the use of shot peening equipment and centrifugal force systems.
The incorporation of abrasive media, such as steel shots, in shot blasting machines allows for tailored solutions to meet specific requirements, such as those for a bucket elevator or blast cabinet. These tools ensure quality control across various industries at competitive prices, supporting sustainability and fostering trusted partnerships for future development.
Choosing the Right Shot Blasting Equipment
When it comes to shot blasting equipment, specific applications and materials are important for achieving optimal performance. Different industries use shot blasting for tasks like cleaning metal components, removing impurities, and polishing metal. The right machine will depend on the type of abrasive media, such as steel shots, and the desired surface finishing. Features like the blast wheel design and the compressor capabilities can affect the blasting process and operational efficiency.
For example, centrifugal force in wheel blasting can enhance metal strength and durability. Selecting a reliable manufacturer is also important. They should have a proven commitment to quality and provide quality control during production. Services such as maintenance support and customized solutions can ensure long-term customer satisfaction.
Evaluating these factors can make a buyer a preferred supplier in various industrial applications and contribute to sustainability while keeping machine costs affordable.
Top Tips for Operating Blasting Machines
Operators should start by wearing proper safety gear and familiarizing themselves with machine controls for the safe usage of shot blasting machines. Regular checks on components like compressors and separators will help maintain the equipment. Operators can also inspect the blast wheels and bucket elevators to ensure they are functioning correctly, minimizing downtime.
To prolong the lifespan of blasting machines, conducting routine quality control checks and addressing any wear on parts promptly is important. For optimal performance, using advanced technology and quality abrasive media can improve efficiency in the blasting process. Following best practices, such as adjusting the angle and distance of the blast cabinet, can enhance surface finishing. Understanding metal components and their properties, like metal fatigue and surface hardening, will guide operators in producing customized solutions for various industries.
Consistent polishing of metal with steel shots and ensuring proper airflow with compressed air help remove impurities effectively and contribute to sustainability and customer satisfaction while maintaining affordability. A trusted partner, offering a wide range of sand blasting and shot peening equipment, can assist operators in achieving superior results and operational efficiency.
Future Trends in Shot Blasting Equipment Solutions in India
Emerging technologies are transforming shot blasting machine solutions in India through innovative designs and materials. Manufacturers are focusing on advanced technology, such as modern compressors and blast wheels, to enhance the blasting process. These innovations provide improved resistance to metal fatigue and surface hardening, boosting the durability of metal components.
Sustainability initiatives are gaining traction, emphasizing eco-friendly abrasive media and energy-efficient equipment. Such solutions effectively remove impurities while ensuring operational efficiency, making shot blasting and sand blasting machines more environmentally conscious.
Additionally, automation is anticipated to enhance effectiveness. Automated systems can deliver better quality control and consistency during surface preparation and finishing, leading to greater customer satisfaction and enabling customized solutions for various industries, all at competitive prices. Equipment like bucket elevators and blast cabinets can optimize operations, establishing manufacturers as reliable partners for efficient and safe abrasive blasting practices.
Conclusion
Shot Blaster is a top provider of shot blasting equipment solutions in India, offering a wide range designed for various industrial needs. The company’s products include shot blasters, grit blasters, and other surface preparation tools suitable for applications such as cleaning, deburring, and surface finishing.
Prioritizing innovation and efficiency, Shot Blaster features advanced technology that enhances performance while reducing environmental impact. The equipment is built for durability and reliability, ensuring a long service life and consistent results in demanding operational settings.
Beyond high-quality products, “Shot Blaster” offers outstanding customer support, including installation, maintenance, and training services. This dedication to service helps clients achieve better performance and improve productivity.
Shot Blaster’s solutions serve numerous industries, including construction, automotive, aerospace, and manufacturing, positioning the company as a significant player in the Indian shot blasting equipment market.
FAQs on shot blasting equipment
What types of shot blasting equipment does Shot Blaster offer in India?
Shot Blaster offers a range of shot blasting equipment in India, including portable shot blasters, automatic blast machines, and dust collectors. For example, customers can choose from the Shot Blaster for small projects or the Airo Shot Blast for larger, industrial applications.
How can I choose the right shot blasting equipment for my needs?
Assess your project requirements by considering surface size, material type, and desired finish. For delicate surfaces, choose a fine media and lower pressure system; for heavy-duty tasks, select robust equipment with larger media. Consult manufacturers for tailored recommendations and review user testimonials for performance insights.
What are the advantages of using Shot Blaster’s equipment compared to competitors?
Shot Blaster’s equipment offers superior efficiency, with faster surface preparation times and reduced dust output. For example, our models can complete a job in half the time compared to competitors, enhancing productivity and ensuring cleaner work environments. Enjoy reliability and support with our industry-leading warranty services.
Does Shot Blaster provide maintenance and support for their shot blasting machines?
Yes, Shot Blaster offers maintenance and support for their shot blasting machines. They provide regular servicing, troubleshooting assistance, and spare parts availability. Customers can contact their support team for scheduling maintenance or accessing technical resources online.
Can I get a demonstration of the shot blasting equipment before making a purchase?
Yes, you can schedule a demonstration of our shot blasting equipment. Contact our sales team at inquiryi46@gmail.com or +91-8094701127 to arrange an on-site demo or a virtual presentation. Additionally, visit our website for video demonstrations and customer testimonials.